Covid-19 Pandemic and Global Supply Chains – Lessons Learned from Executives
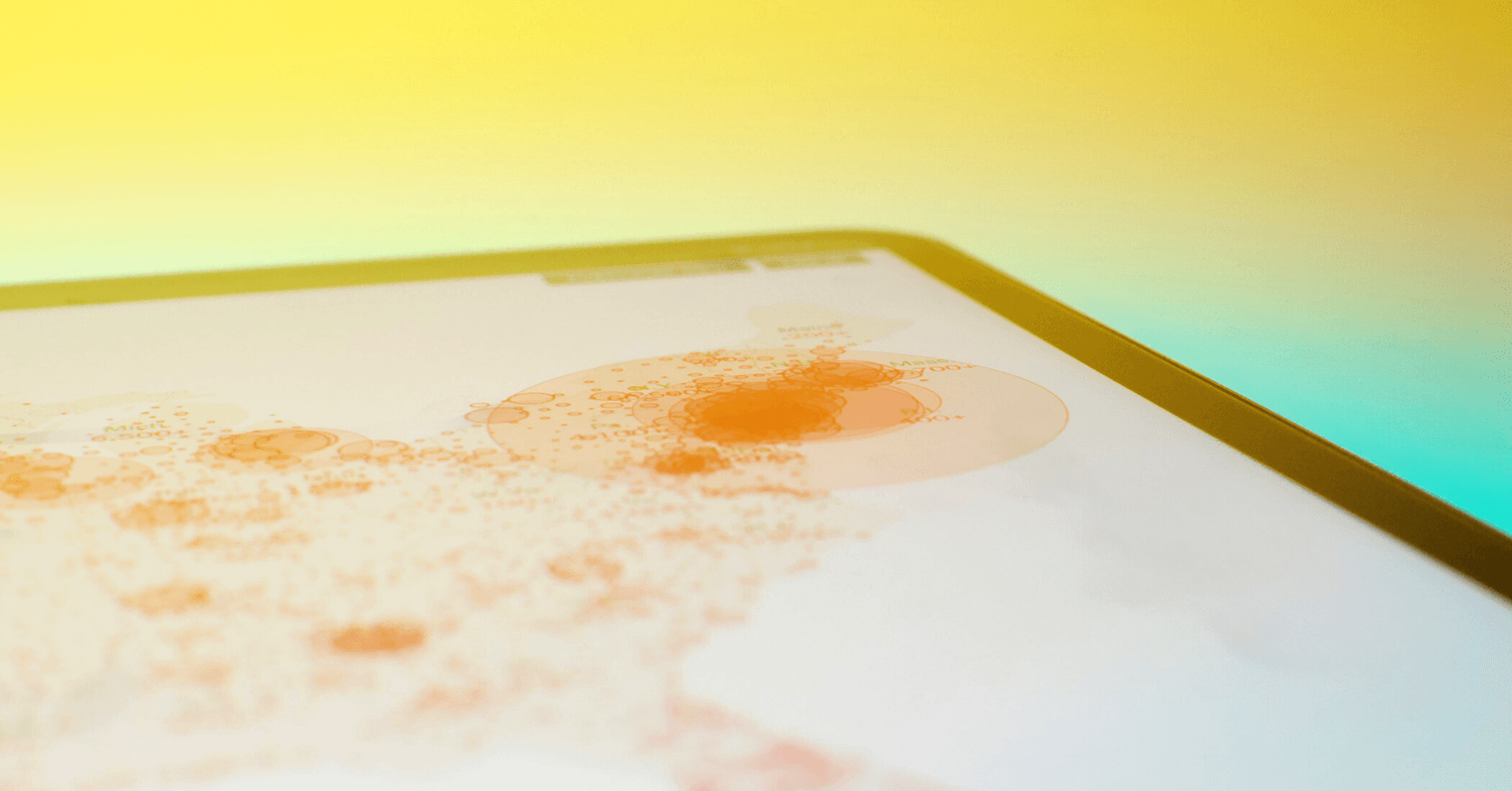
What are the effects and how to prepare for the disruption?
The manufacturing companies around the world are facing Covid-19 pandemic with two anxieties: How will the coronavirus effect on their economy and business continuity, and how should the leaders prepare for the disruption. We interviewed 12 leaders and executives operating in the manufacturing supply chains and asked their insights for this topical challenge.
Obviously, one of the unitive factors is decreased demand. During the latest decades, we have been witnessing that the demand for manufacturing companies (delivering investment goods such as machines and equipment) often increases and decreases hand-in-hand with the general economic trends. Investment goods are purchased when there is a hype of construction and production industries. The decrease in demand has often dramatic effects leading to employee layoffs. The companies we interviewed have all needed to plan or activate reduction of workforce. In some companies, white-collar staff is currently working 60 % – three days working week.
The availability of components
In these times, the biggest headache for a supply chain professional is to ensure the strategic components for own production and assembly. The production in manufacturing companies has been built to rely on accurate component deliveries from global supply chains. The coronavirus substantially hit this trimmed system. Consequently, the trust in global supply chains has reduced during the latest months.
During the past years, global supply chains have become extremely complex. The target for the companies has been to produce the end-product in the most cost-effective way. When this kind of crisis occurs, the monitoring of a complex supply chain and transparent delivery control gets nearly impossible. It doesn’t help purchasers and suppliers if the operations are done manually and interaction is still in email inboxes.
The experiments related to operations in China revealed problems in deliveries and logistics. The interviewed leaders started to notice deviations on delivery accuracy. It led to different manual procedures to monitor the shipping and progress of deliveries. Second perception was the lack of containers. A huge amount of shipping containers stuck in China which caused a significant problem for logistics planning. Another logistical problem has been the uncertainty of the airfreight – is the air cargo available and how much does it cost? The price can be 500 % bigger than prior to coronavirus.
Some smaller companies see that it’s easier for bigger companies to face a crisis. It’s explained with a stronger balance sheet and solvency that smaller companies often don’t have. Those companies, which have a possibility to strengthen their reserves and fill up the warehouses, are purchasing strategic components and materials with increased volumes. Being a small volume customer to a supplier is a challenge when the availability of the goods is poor. Supplier is more eager to serve the customers with bigger volumes. In these circumstances, a deep, proper and reciprocal supplier relationship get highly valuable.
The strategic scenarios
The nature of strategic planning has changed tremendously after the outbreak of the Covid-19 pandemic started. The long-term scenarios must be reshaped with an uncertain understanding of how the crisis evolves and how long it lasts. The scenarios must also be set for geographical areas. How can our own and suppliers’ factories operate and deliver in China, India, Italy, France and Spain? This is something that companies need to follow and monitor on a weekly basis, some say even on a daily basis.
Because of the past long-term development towards very complex supply chains, it’s extremely difficult to execute big changes in a short time. To change a strategic component supplier to another is not an easy nor affordable exercise. The experts see that the production volumes will remain where it’s the most cost-effective to run the production. The challenge is how to establish an enduring supplier network to maintain the supply chain agility in times like this we’re living now. It’s very hard to establish and ramp-up the network during the pandemic because it’s nearly impossible to run audits for new suppliers. Auditing procedures should mainly be done physically at the suppliers’ site. Finding a second source supplier for all critical components is a common topic in discussions right now.
None of the European manufacturing companies we interviewed see that the volumes could be transferred from Asia to Europe in a short-term. But nearly all of them see that there should be a capability to purchase more from the suppliers located nearby – which often are the second sources already. At least, how to handle the “China risk” will be on the table of many European companies. It is obvious that European manufacturing companies will decentralise the production to lower the supply chain risk. Production will be diversified more heavily between the primary and second source suppliers.
Supply chain monitoring
When the crisis occurs, a lot of effort, time, and resources are put on supply chain monitoring. Many companies have started to monitor their supply chain with different values. Especially the strategic suppliers are in a daily-based monitoring. In general, Covid-19 has become the most common reason for delivery delays. Therefore, the most typical monitoring objects are the progress of deliveries and the financial situation of the supplier. The main target for monitoring is to ensure the deliveries and identify the bottle-necks. It’s easier to help the supplier when the problem is identified in an early phase, for example, the actions when the supplier is facing a financial destress.
The focus of monitoring is directed especially on the sole and single-source suppliers. A sole source supplier is the only vendor who can provide you with the particular component, system or material you need. If the sole source supplier fails, it can make your supply chain very vulnerable in circumstances like this. We all know the benefits and disadvantages of operating with the sole source suppliers but the crisis like pandemic can escalate an unexpected handicap and roadblock for the strategic deliveries. Therefore, the short-term scenarios and tactics should be monitored and analysed on a weekly or even daily basis.
Daily-based detailed monitoring management in manufacturing companies has become usual. Especially the bigger companies have established task force meetings which have a structured agenda. Taskforce meeting is a forum where the people working in procurement can discuss the challenges and learn from each other. The latest conversations cover which supplier’s factory is closed and which supplier can replace the deliveries. There are also several new requirements from the public authorities that need to be fulfilled and the task force meeting gives an excellent forum to handle together these issues as well. The supply chain professionals are generally quite surprised how successfully the digital gatherings have worked out.
The significance of up-to-date information has increased during the pandemic. It’s difficult to allocate the components and prioritise the deliveries without up-to-date information. Companies which have implemented digital tools and solutions are cutting edge. The monitoring is way more time-consuming if you don’t have the digital capabilities in place. It’s nearly impossible to gather real-time data manually with emails and phone calls when the company is operating globally in many different countries. In the middle of the email hassle, it’s hard to make good decisions, especially in these times when you need to take over your colleagues’ work tasks as well.
Companies which have digitalised their supply chain processes don’t need to chase the suppliers as much as those who need to do the monitoring work manually. When operating with limited resources, it’s crucial to spend time on value-adding activities. Digital solutions increase this capability considerably.