How can manufacturing companies respond to the coronavirus?
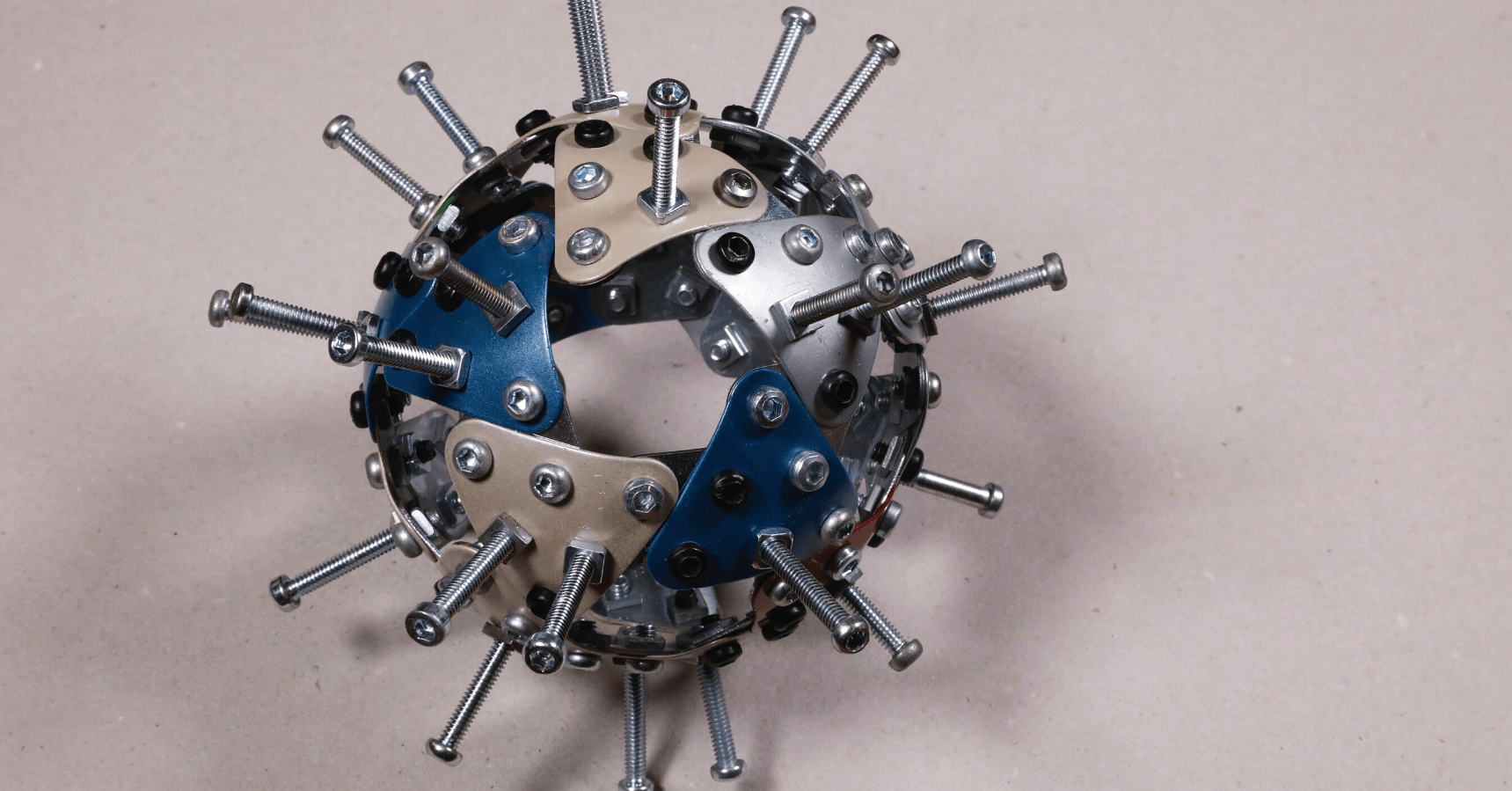
The crisis is putting global supply chains into a hard stress test
While first and foremost a human tragedy, loss of life, threatening our safety and health, COVID-19 pandemic is challenging the global economy as well and putting the supply chain operation into a hard test. All people and companies around the world are facing novel uncertainty and tremendous impact in their daily lives and actions.
In a very short time – just past few days and weeks – companies around the world have implemented their crisis strategies. Purchasing volumes are re-allocated. Two-way communication between customers and suppliers has been strengthened. On forecasting practices and co-capacity planning have been sharpened. If possible, the warehouses are filled with critical components. Production facilities have been isolated as a red zone. Only the employees working in the production have access to the facilities. The working shifts have been re-organized to avoid the outbreak of the infection. Employee backup plans have been updated and implemented. All the travelling is disallowed. Face-to-face meetings are turned into online sessions. Seminars are cancelled. White-collar workers are told to work remotely from home.
It’s obvious that all workers in manufacturing ecosystem are not able to work remotely. But nearly all white-collar workers can do that. Companies have had different policies and recommendations for remote work, but now all companies are forced to take a digital leap, whether they want it or not. Coronavirus does not ask the CEO’s opinion. We’re facing a stress test of working remotely in all communities and the ways of working will change, permanently.
If the remote work is led properly, it can boost productivity as employees skip their commutes and avoid workplace distractions. There’s also lots of evidence to prove this. Remotely working companies believe that their ways of working attract a more talented workforce, and increase the staff wellbeing and productivity. But it’s not a simple trick to jump quickly into a remote mode. To succeed, you need to establish simple rules which everyone can and must follow.
Remote working tools have developed considerably during the latest years. Teams and Slack have become familiar as remote conversation tools. Enterprise platforms such as Asana, Dynamics 365, Jira, Salesforce and SAP are providing a common digital office for all employees whether they are working in the headquarters or far away somewhere else. Vertical platforms, such as Jakamo, are serving certain industries to solve problems in specific solution areas. It’s crucial to choose the right tools and use the full potential.
Remote work has become mainstream
Suddenly, we all are recommended and ordered to keep social distance with each other. That’s why the working remotely has become mainstream in a very short time in all communities. Even the team leaders who didn’t think they could manage their team online only need to adapt to this exceptional environment.
If you are arranging a meeting or a workshop with several participants, make sure there is a facilitator in place if you don’t do it yourself. In a workshop, the facilitator is always responsible for three things: 1) ensure the results, 2) take care of the schedule and 3) enable a rich dialogue. These three responsibilities are even more crucial when working remotely.
I got a great tip from one of my colleagues who advised me to communicate with hands and spontaneous facial expressions even if the camera is not on. The other participants will feel your body language positively thru your voice.
Demolish the silos – build networks
During the latest 30 years, the global economy has become networked. Nowadays the value is created in business relationships and the companies are working in ecosystems. In the supply chain, there are three main flows which companies need to manage smoothly: 1) Goods & service flows, 2) capital flows and 3) information flows.
Two first flows mentioned have crushed the traditional hierarchical systems and moved towards networked operations. It’s encouraging to see that the third flow is following the same trend. The information flows are finally moving from silos into networks. The digital transformation of information sharing in the supply chain has truly begun and the platforms are here to stay.
In recent years, the common requirements to operate effectively in a business relationship have become action traceability, transparent real-time data and ongoing communication. When companies are operating in crisis and uncertain circumstances, these requirements are even more crucial. Platforms serve ecosystems and fulfil these requirements a lot better than the traditional company-specific portals. The data and interaction are available and visible even when the boundary spanners – the workers – are not available for work. The relevant data is yet available and seamless operational execution is still possible.
While keeping each other safe and healthy, I encourage all companies in manufacturing ecosystem to utilize the full potential of digital solutions. It increases the safety of your community, supports public health, speeds up sustainability and keeps operational execution ongoing.