How to get started with supply chain risk management?
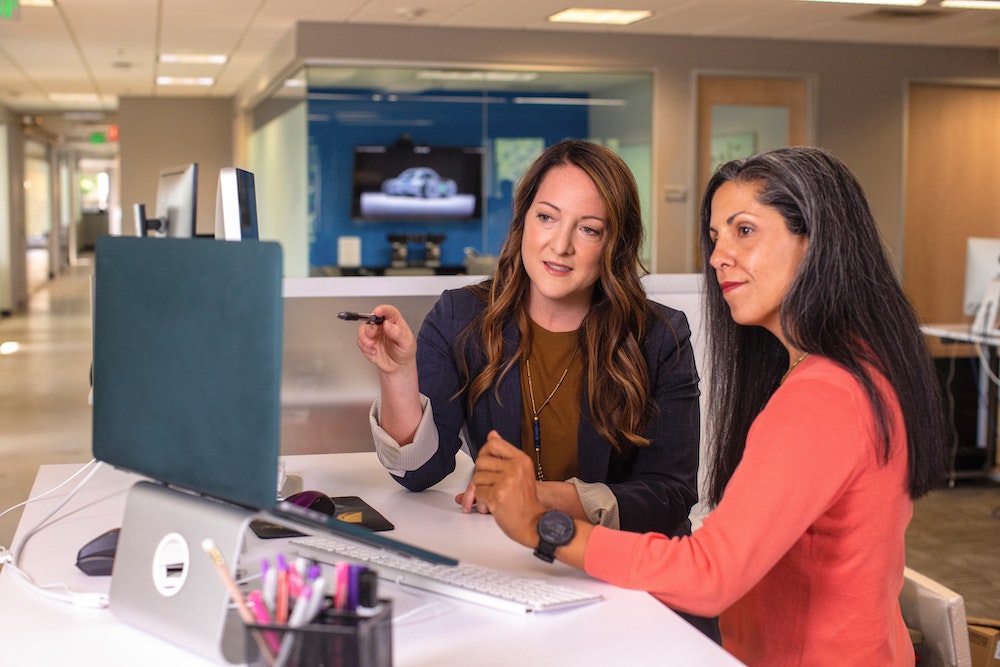
Value chains are complex and vulnerable in nowadays’ networked business ecosystems. Manufacturing companies are highly dependent on their suppliers e.g. in terms of costs, quality, sustainability, technology, availability, and lead times. For instance, 80 % of the company’s costs or sustainability impacts are commonly coming from purchases.
The global pandemic and the Ukrainian war are unaccountable humane crises. Besides, they have had an exceptionally big impact on supply chains in many ways. Many unlikely risks have been realized in the supply chains and we have seen significant availability problems, extremely long lead times, and multiplied prices. At the same time, many manufacturing companies have closed their operations in Russia (the only proper thing to do) and lost a big part of their markets.
No one could probably have been able to foresee these crises coming and these risks realizing at least at the actual scale. Anyhow, many companies probably could have been better prepared for these or any other upcoming supply chain risks.
What procurement executives could do to prepare for the next crisis?
There are at least three concrete digitalization-related ways to start progressing with your supplier risk management.
Automate manual work & go strategic
Firstly, there is not enough time for strategic development work that is the base for supply chain risk management. According to our research, approximately 50 % of the working time of an operative purchaser in a typical manufacturing company is spent on non-value-added manual work.
This manual purchase order process-related work can be easily automated by a supplier experience platform. In that case, purchasers’ focus can be changed from operative manual routine work more towards strategic and development-oriented work. Think about what your team could reach if all members would have 4 h per day for developing supplier relations, building resiliency, and analyzing and mitigating the risks together with the suppliers. Most probably you would be much better prepared for future risks.
Build visibility & improve communication
Another typical problem in manufacturing companies is the lack of visibility and communication at the operative level. If something happens, you need to be able to see what is going on with the deliveries from your suppliers. Besides, you need to have easy ways to communicate (not email) with the suppliers to solve challenging situations in collaboration.
Visibility can be built and communication improved also via digitalization by implementing a supplier experience platform.
Know your suppliers & develop together
Another typical problem in manufacturing companies is that they do not have a comprehensive view of their supplier base. For instance, compliance or supplier risk-related data is scattered to multiple excel files and individual mail inboxes. When something unexpected happens it is difficult to know which suppliers are impacted and what alternative suppliers there could be in the company’s supply network. Besides, when you know your supplier’s capabilities and risks better you can start working together with them to improve.
Luckily, the supplier master data (including compliance and risk management) can be also easily digitalized to enable open compliance governance between your company and the suppliers.
Why you should start today?
The next crisis is coming for sure. The world is very uncertain at the moment and supply chain risk management is more important than ever for being prepared for the next crisis.
By utilizing the supplier experience platform a manufacturing company can release purchasers’ time to work with supplier risk management and improve the visibility and communication at the operative level. In addition, it will enable a much better and more modern way to manage the supplier base’s compliance and risk and develop resiliency together with the suppliers.
Even under all the supply chain-related acute problems and pressures, manufacturing companies should think more about the future and the time perspective should not all time be weeks or some months. It is not difficult or expensive to get started, but the impact can be huge. There should not be excuses to wait and do nothing.