How to succeed in delivery project? Avoid these 3 mistakes!
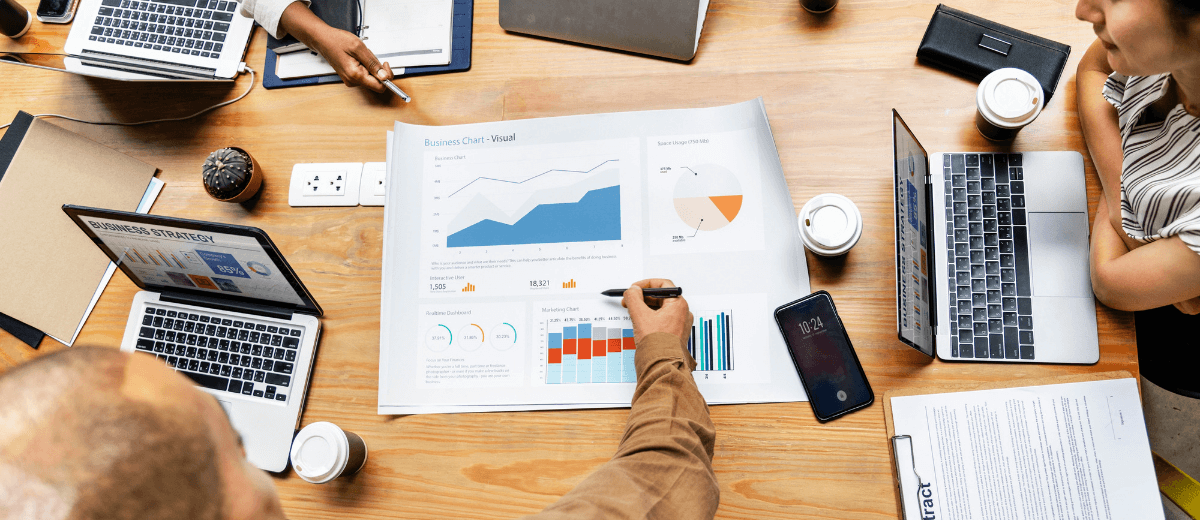
Every project manager knows, that both the small-scale equipment deliveries and complete turnkey projects have their dark and sunny sides. Professionals in both extremes struggle with changing requirements, variety in company culture, processes and tools, and the complex network of suppliers. This struggle sometimes delivers unpredictable and poor results.
I have had a privilege to work with the best partners in the industrial delivery project scene. Project offices, project development initiatives and project sites have been excellent places to observe, what it takes to successfully deliver an animal called ‘a project’.
We have used information biased project maturity models to investigate the different organisations and different delivery project dimensions (schedule, cost, quality, content etc.). And we learned a bit of the characteristics of projects.
When mapping PMOs and project organisations, there seem to be plenty of indicators why projects tend to slip to the dark side. Here are some of my favourite flaws, which mess the delivery projects:
- Information does not flow
- People (or lack of common process)
- Tool mismatch
- Heavy cost control need, but no tools or resources for that
- Relying too much on customer quality assurance
Let’s focus on the first three ones:
Mistake 1: Information does not flow
Lack of information model leads to issues in missing, false and overlapping information. A typical example is that project has defined a clear “hardware” specification (bill of material) for suppliers but has not defined required information. As a result, project information does not have scope, schedule, cost nor quality criteria at all.
This can initiate from a customer, who is not able to define the information requirements – but expects and needs information deliverables. A conflict, that is easy to solve by proactive planning, getting the customer approval for information too and ensuring the flow of information during the project.
Most project organisation tend be ad hoc or reactive in managing their project information. PMI (Project Management Institute) research states that 56% of project risks are directly related information flow issues or poor communication. Apparently, those must be mitigated. So, specify what your project information is, when and how it should flow. Manage and measure it. Mistake avoided.
Mistake 2: People (or lack of common processes)
Repeating tasks and projects bring efficiency and profit. Reinventing the wheel in every project does not. People without a process tend to reinvent and change bits and pieces a lot. When projects or project tasks cannot be grouped, compared or measured across your project portfolio, alarm should go on.
A good project manager can cope with the tough projects. Every company should have these “superheroes”. But when the organisation grows, number of potential superheroes increase and alignment issues step in. Projects tend to invent their own best practises and start to sub-optimize. This is first noted in the sibling and child functions (e.g. sales, sourcing, partners and suppliers) and finally in the management too.
The result may occasionally be good, but nobody knows why. Even the project manager cannot always explain why project #1 shined and #3 failed. He is like a student in math class, who knows the right answer but does not know where it came from.
Projects delivered with a common process usually know the success formula: There is a clear assignment of project responsibilities. Project model consists of a common set of tasks, that can be repeated throughout the project portfolio, measured in form of effort and cost, and finally optimized and automated.
Easy to say – hard to implement. The mapping of project organisations exposed the biggest variance in maturity of ‘people and processes’ dimension. Some have done their homework and are good, and some have a lot to improve.
Mistake 3: Tool mismatch
Project professionals have love & hate relationship with technology. We create and breathe the technology, but it has (in form of systems and applications) tendency to live on islands where one island delivers us oranges and the other one delivers apples.
Within single organisation a project manager can end up collecting data from several different systems and reporting to another set of applications. No wonder that PMI study states, that 85% of PM’s time is spent in communicating and collecting data.
It does not ease the situation, that customers and suppliers have probably another set of systems and applications which is multiplying the need of conversions and knowledge. It also blurs the project transparency and complicates the information flow (See mistake 1).
Since this (tool mismatch) seems to be nature of project business, it is impossible to avoid it completely, but mature project organisations have succeeded in this by following few principles:
- Minimizing the amount of overlapping systems and applications. Like people, applications should have their assigned responsibilities too. If duplicated silos exist, they have their role as a master or slave of data.
- Facing the facts: There is no one system to rule them all. Mature organisations have developed their common PM system with integrations to other internal islands. And they have also a strategy to connect, collect and share data with external systems (customers and suppliers).
- Platform thinking. Utilizing common platform in connecting and sharing data, automating processes and business models.
The consumer business is leading the game of utilizing technology, systems and applications. John Mancini, an AIIM-evangelist, flamed the difference: “When a Millennial starts in a project organisation, he thinks he came into a computer museum!”. That sums up well how far we are in terms of usability and digitalisation of project business. But the good news is, that there are points of improvement.