Reflecting digital transformation as a Six Sigma practitioner
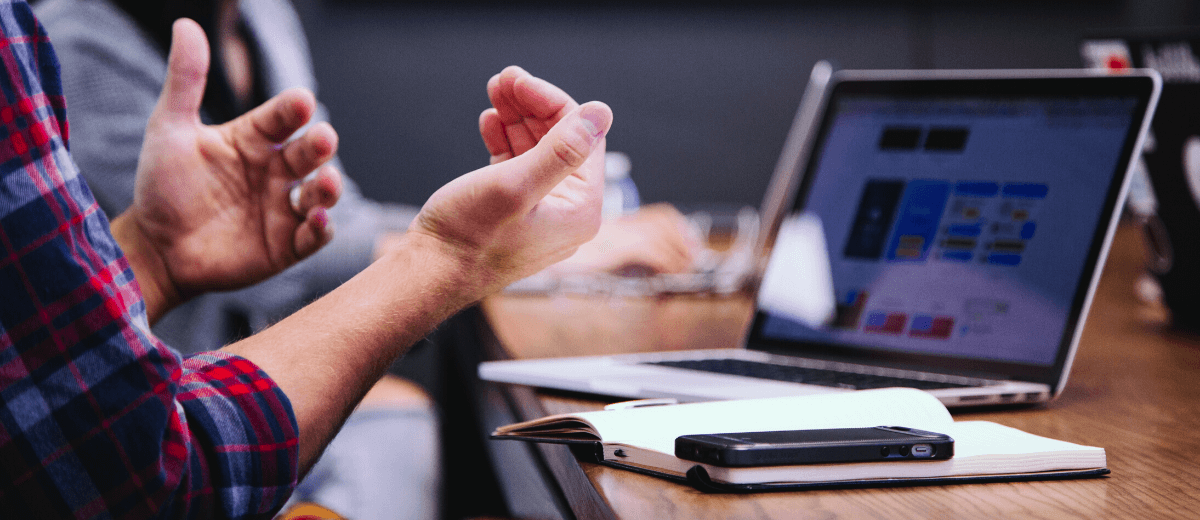
How to get loyal customers and free beer as an SCM project take-away
One of the most memorable customer experiences happened to me in my early career back in Germany in 2011. I was working in our Technical Customer Service Team as a project manager for a multinational paper company. I was young, green and very keen to prove myself, but could not, in fact, comprehend the massive scope I was facing. We were given an opportunity to work with a key customer and myself leading our Lean Six Sigma project. The assignment was to improve the entire supply chain performance from paper manufacturing to a printing house. However, as a result, we made a loyal customer and a process innovation tied to the story was patented in Sweden. Now reflecting the digital transformation over the past decade based on my own hands-on experience in operations development many things have become easier, better or smarter hence industry productivity keeps going up thanks to the Internet of Things.
Having a meaningful dialogue with the data is fundamental
What a feeling right after the customer’s project team gave me a case of wheat beer from the world oldest brewery as a project token. Instantly, I learned the valuable lesson of the impact of really understanding the customer’s value-proposition and the effect that solving the customer’s problem leaves on the manufacturing shop floor. Lean Six Sigma philosophy as any data-driven business nowadays requires a great deal of data for making fact-based management decisions and delivering bottom-line results.
In the perspective of modern Industrial IoT era, above all rapid merge of connectivity and novel sensing methods, our operational environment looked somewhat a “Jurassic Park” in the beginning of the past decade. A big thanks to incredibly systematic German operations crew and laboratory services for massive manual data collection, which was essential for Minitab analytics and eventually for whole project success. Hence, having a meaningful dialogue with the data requires first and foremost quality. The data quality was and is still today fundamentally critical since bad quality data will jeopardizes process modelling tied to performance improvement. Only after that, we can focus on the access and availability of the process data. Do you still doubt the well-known slogans of the German way of working?
Writing the future of manufacturing with Artificial Intelligence
My mentor told me once that generating at least triple savings in comparison of your annual salary means you have managed to hit your yearly target. At this time, when elaborating her statement I am wondering if my breed of Lean Six Sigma practitioners will become obsolete one day by giving the mandate of operations performance to Artificial Intelligence? Also, it becomes evident that anymore we cannot handle the Big Data alone in the factories and I see the urgency for Remote Services due to more and more data is simply available and tremendous cost related to “manual labour”. Therefore, we need a power of Cloud Computing, machine learning for data processing with high domain knowledge to understand variations of key process inputs and outputs on-line tied to critical to customer requirements.
After all, I am very excited about the current reality possesses to elevate process entitlement in any given manufacturing industry. Yet, I would not make fully autonomous processes due to safety reasons for instance, but who knows how the famous Homo Deus will write the future.
Count your blessing and carpe diem!