Supply chain collaboration – Another buzzword or something else?
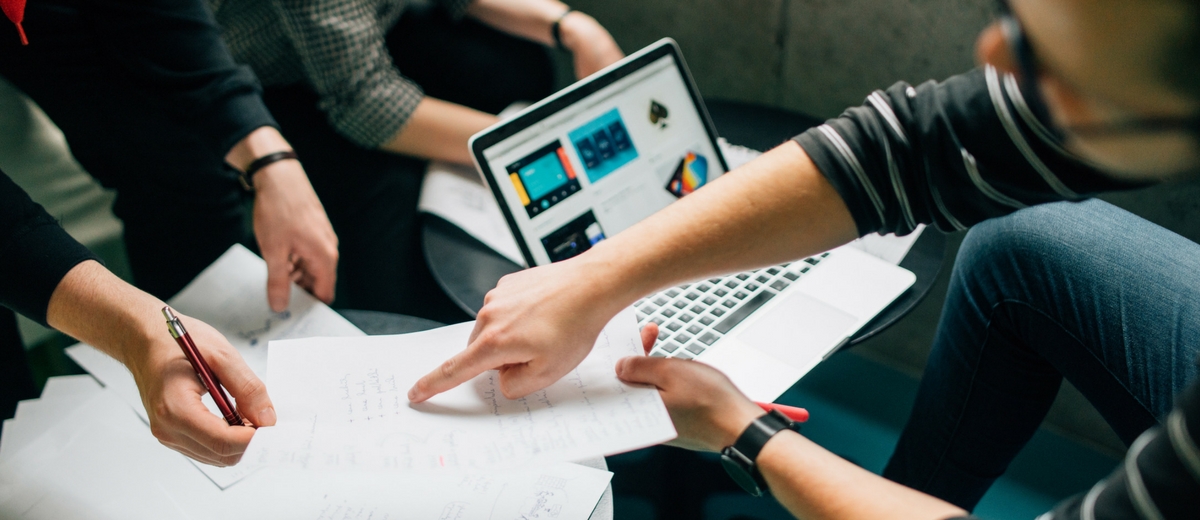
This blog post was published originally in Jakamo Official Blog on 30 January 2015
Cost reduction. Now there’s a pair of words you’ve heard a lot since last decade no matter with which function you’re working with in a business. I don’t really like the saying since it has a negative tone in it and is a kind of a signal that we need to use the cheese slicer a bit here and there, slice by slice. I prefer something like value stream optimization or resource optimization instead. Is it something that can be achieved with Supply Chain Collaboration? Maybe and yes, I think we can call it SCC as we all love these acronyms, but let’s find out.
I’d argue that the ultimate goal of business anyway is not to offer something cheap low-value product or service which is eventually an outcome of this cost-cutting strive, but actually optimized value offering which meets customers value expectation. Cost and price is only one part of the equation.
Now this SCC. What it is, what it enables and how it fits here. I would claim it’s not driving cost reduction, but instead increasing value with your (not suppliers, but) partners without utilizing more input resources. Let’s look at what is really written behind those words. Let us take definitions from Wikipedia, as I know that they know what there is to be known from known things over there.
COLLABORATION is defined as working with others to do a task and to achieve shared goals. What is more rewarding than reaching a goal? I would say it’s reaching a goal with someone else, with a partner or a team with whom you have shared values, vision and goals. But hey, I am a team player, go ask from some individual artist or sportsman and he could claim the opposite, and I would argue that it was still a team effort!
A SUPPLY CHAIN, on the other hand, is a system of organizations, people, activities, information, and resources involved in moving a product or service from supplier to customer. It can be a very complex system with multiple tiers of companies in a network, needed to be working on the same pace towards same goals in order to fulfil the needs of the final customer or consumer.
Considering these, I could define SCC as something like a method to utilize the know-how of your partner companies and optimize the resource utilization in your supply chain to increase end customer value. Now that became too long, maybe you could come up with a better version?
Anyway, to drive supply chain collaboration one should have a mutually respectful approach, meaning there are a couple of prerequisites that should be in place:
- See your suppliers as partners in value creation, not as your “suppliers” or “minions”
- Foster trustworthy and openness in cooperation with your partners
- Invest in developing and training your supply chain
- Use the carrot instead of the stick to recognise good performance and align the objectives
The outmost importance anyhow, in the end, is communication between the companies and within the entire supply network. As important is that the information that is being shared is managed properly and that required information is readily available in the business context to anyone who needs it and can contribute to it.
On my next posting, I’m planning to further introduce the concept and how supply chain collaboration can be utilized as a strategic tool to increase end customer value. Meanwhile, let’s collaborate, so share your thoughts and ideas. Is it another buzzword or something more?